Microwave Absorbers — Types and Selection
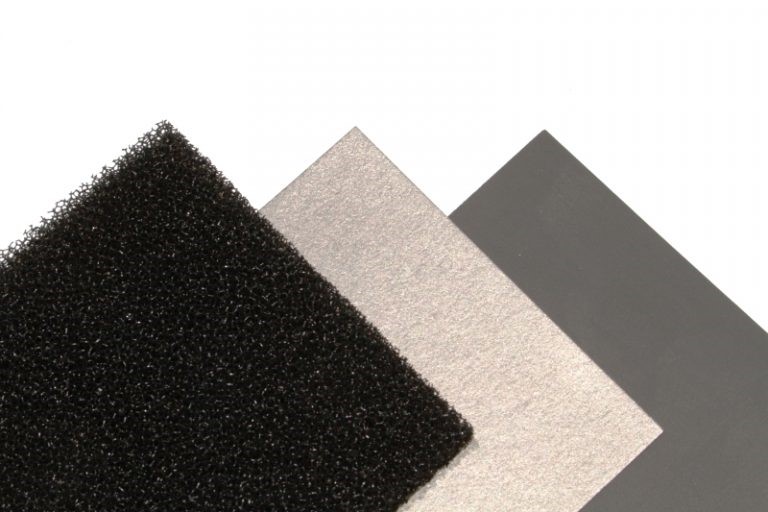
Is a well-designed circuit board not operating properly even after incorporating a shielded cavity? The reason can be ‘resonance’ — a phenomenon that can negatively affect the performance of a circuit board, which in turn hinders the overall performance of a system. Such problems can be addressed by introducing a microwave absorber in shielded microwave cavities. Microwave absorbing material can eliminate both simple and complex cavity resonance and protect the system from short-circuit.
With the increase in processor and clock speeds, the emitted frequency also increases. Standard EMI shielding materials like board-level shields, fabric over foam and finger-stock lose their effectiveness at such high speeds. It is found that these materials even contribute to the problem of resonance by providing a conductive path for the energy, thus retaining it inside the cavity. In such scenarios, microwave absorbers prove to be useful in absorbing frequencies ranging from 500 MHz to 77 GHz.
Microwave absorbing materials are generally of two types: magnetic resonant frequency absorbers and graded dielectric materials. Resonant materials can absorb multiple frequencies and provide better environmental resistance. While determining which type of microwave absorber to use, you should consider the physical, electrical and application parameters of the material. Also consider desired effects which may include cavity resonance reduction, insertion loss, reflection loss and surface wave attenuation. If you are going to utilize your application in protected environments, opt for graded dielectric absorbers.
This type of microwave absorbing materials is designed to absorb energy at single discrete frequency as well as multiple frequencies. To make these materials absorb multiple frequencies, you need to control the critical magnetic and dielectric loading along with the thickness of each layer. Magnetic resonant frequency absorbers use the process of phase cancellation. While a part of the incoming wave is reflected, the rest is transmitted by the absorber. The transmitted portion of the wave again undergoes multiple internal reflections, thus giving rise to a series of emergent waves. The sum of the emergent waves equals in amplitude to the initial reflection portion. While according to theory, there is zero reflection at the design frequency, in reality there may be absorption of >30 dB.
The most common type of magnetic resonant frequency absorbing material is distributed magnetic fillers suspended in a flexible elastomeric matrix. The principle of phase cancellation states that the lower the frequency to be attenuated, the thicker the material should be. So how can you make the material thinner? Increase the permeability and permittivity of the elastomer. This will help raise the refractive index and you will attain the desired thinness. Also, iron, ferrites and certain alloys are used as fillers to increase the permeability of the base material. Depending on the frequency for which these absorbers are optimized, common thickness range is 0.020″ to 0.175″.
Graded dielectric absorbers require a steady tapering of impedance from a free space to a lossy state to achieve absorption. With little initial reflection, a material with adequate transition from free space to lossy state can provide high attenuation. The most common absorbing medium is a conductive carbon coating over a polyurethane-based foam substrate. Materials having <1/3 wavelength thickness can achieve high levels of reflection loss, even better than 20 dB. Popular dielectric absorbing materials include plastic, foam and elastomers, which are non-magnetic and have a permeability of 1.
Microwave absorbing materials have established their importance in the field of EMI shielding. Earlier, microwave absorbing materials were used by the U.S. military to reduce the reflections of high-frequency energy. However, using microwave absorber for commercial applications has become a trend with the increasing clock speeds in smart electronic devices. No wonder, more and more service providers in the diverse fields of consumer electronics are adopting this technology.