Lights-Out: Manufacturing In The Dark
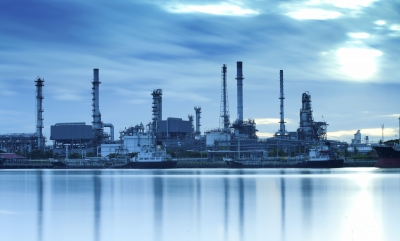
At first blush, lights-out manufacturing sounds counterintuitive. Cutting the lights on a manufacturing floor seems like an extremely bad idea. But that’s not always the case, as several companies have discovered. What do you do if you’re a small manufacturer trying to produce more with greater efficiency? You automate and turn off the lights. From electronics to injection-molded prototypes, if you create a large volume of goods, you can find a way to benefit from the lights-out model. You just have to make sure you handle it correctly. Do your homework before you roll anything out and you’ll be able to scale up your output without dramatically increasing your payroll.
Lights-out manufacturing is the process of automating as much of the manufacturing process as possible — so much so that the machines require little, if any, human interaction to produce goods and parts. A company that implements lights-out manufacturing can leave its machines unstaffed the majority of the time without losing productivity. Roger Smith, former CEO of General Motors, coined the term lights-out in the 1980s. The practice allows companies to turn off not just lights, but HVAC systems as well.
Lights-out primarily helps increase efficiency. Computers are far more precise than humans, especially for repetitive tasks, and they don’t tire, so they can do more work more reliably than humans can in the same timeframe. Some companies, like Makuta, a micro molding manufacturer, operate with only one manned shift, but create products 24/7. This reduces overhead by requiring a smaller staff, saving the business operating expenses and removing a large element of human error. The machines operate themselves most of the time and don’t make mistakes as long as their operators program and maintain them correctly. Vanderhorst Bros., a machining facility in Simi Valley, CA, can run its machines for days at a time unattended. Most of the work performed by humans is attending to the machines’ needs, unloading finished products and refilling raw materials.
If the prospect of running your facilities 24/7 intrigues you, you’re not alone. What was once a pipe dream — GM’s efforts in the ’80s flopped — is now a reality to many companies. Robotics and computing have advanced to the point that ready-made machines have enough flexibility and precision to create most parts with little to no supervision.
There are limits, however. No machine can make everything, no matter how many attachments you buy. To create the level of automation lights-out requires, you need to identify exactly what you can and should manufacture with robots. Only use machines to create things you know won’t change. Make sure whatever your machine is doing is necessary; don’t move a task from a human to a machine without identifying whether that action could be eliminated entirely.
Every manufacturer is different; each one requires different machines and processes, because they create entirely different components. That means there’s no single method for creating a lights-out facility. Absorb the ethos behind lights-out, evaluate what you’ve got now and what your goals are and then create a plan for your shift that’s centered around your company. Nobody outside your business can tell you the best way to operate.
Image credit: anekoho on Freedigitalphotos.net