How To Perform A Successful Warehouse Inventory Count
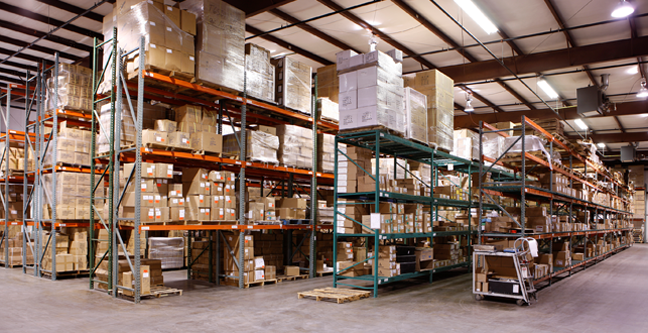
Whether you utilize modern hardware and software for precise inventory tracking and reporting or not, you will eventually have to perform a manual count to assess the state of your warehouse inventory. The reason for this is that software glitches, human error, and other snafus are bound to occur, resulting in actual inventory counts that don’t quite match up to what you have documented digitally. In addition, you need to make sure that occurrences like damage and theft are not throwing your numbers out of whack (and costing you money). If these things happen, you need to know, and periodic counts can help you to find and address such problems. Here are just a few tips to help you conduct a successful warehouse inventory count.
You should probably begin by planning for a shut-down while you conduct your manual inventory. This means cancelling both incoming deliveries and outgoing shipments for the duration of your count, whether it takes just a few hours or a couple of days. In most cases, you’ll want to expedite the process in order to minimize the impact on your operation. After all, time is money. But if you want to conduct a thorough and successful cataloging of your warehouse inventory, you can’t have items coming and going in the midst of your tally.
From there you need to do some prep work to ensure that your inventory count progresses smoothly and efficiently. You should start creating some kind of markers to verify count. As you count items you need to mark them (with tags of some sort, generally) so you can easily see which items have been accounted for and which have not. This can help to ensure that you spot overlooked items and that you don’t count things twice. You also need to create an assignment chart and break your warehouse into sections so that you can send out teams to different areas of the warehouse to take stock of inventory. This will help to expedite the process.
Once you’re ready to begin, you should print up current lists of known inventory. Employees involved in conducting the count will check the items tagged during the inventory process against what is listed in your digital inventory. By the end you should be able to see if your digital count is accurate or if it is off, potentially helping you to find flaws in your system. At the very least, you’re likely to uncover inventory that has been misplaced, mislabeled, and so on.
And when the count is completed and you’ve looked through the paperwork in search of anomalies to investigate, you’ll probably want to perform random checks to ensure that all of your employees reported accurately. If mistakes were made, or worse, employees are engaged in fraudulent activity, random checks could help you to uncover such problems. Just telling employees that you will randomly check results could curb such activities when you count inventory. Don’t forget, this might also be a good time to inspect your storage solutions and your equipment from Heubel Material Handling, Inc. Since you’ll be shut down anyway, you may as well delegate some of your workforce to perform inspection, maintenance, and repairs.