Everything You Need To Know About Cement Clinker Grinding Aids
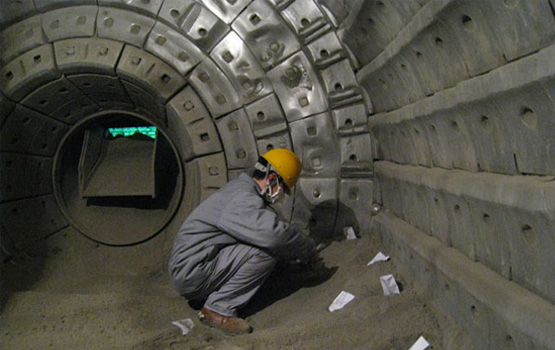
Today’s process engineers face several issues; these range from the need to process more ores, severely limited but increasing energy costs and more. Some of these challenges have made it imperative to add some additives to the grinding plant to significantly improve the clinker grinding process. These additives are what are referred to as grinding aids.
Cement grinding aids were first used in commercial quantities about less than fifty years ago. At the time, they were primarily organic liquids that were employed in minute quantities to either increase the fineness of the product at a particular production rate or to increase the rate of production for a specific product size.
Whatever the case, the enormous benefits of using these grinding aids far outweighed the cost. However, the grinding aids should have no adverse effect on the finished product or the downstream processing.
Some of the common additives include organosilicon, amines, carbon black, urea, glycol, resins, kojic acid, calcium sulphate, wood grease, cod oil, etc.
From experimental studies, it had been shown that the use of grinding additives significantly increase the rate of clinker grinding, improve the production rate and result in a decrease in energy costs and decreased grinding time.
Even though the use of additives was a commercial success in the cement industry, there is still need to have a clearer understanding of how grinding aids work. Much fewer efforts have been put into studying the mode of grinding aids.
It’s is a communication process that results in the formation of a new surface. The energy that is needed to produce this new surface can be significantly reduced if the solid surface energy is reduced. This is the mechanism that is believed to be of the improved efficiency.
The theory of adsorption-induced reduction in surface energy was also extended to explain the grinding aids mechanism in tumbling mills. It was shown that the adsorption of surfactants could only reduce the strength of the material when plastic deformation is necessary for fracture.
Since in tumbling mills grinding requires some brittle fracture, the Rehbinder’s effect would not be what is responsible for the action of the grinding aids. Even for plastically deformable materials, the period of stress is too short in the grinding mill, which predominantly impacts fracture.
Also important is the fact that the crack propagation velocities during impact breakage in a grinding mill are far greater than the spreading speed of the surfactant molecules. Vapours (from liquid grinding aids) that are absorbed by the solid surface cannot even improve the breakage efficiency by reducing the surface energy of the solid surface.
This thus casts doubt on whether adsorption-induced changes in the surface energy are what are accountable for the action of grinding aids.
When molecules of the grinding aid are absorbed on the solid surface, it leads to blocking of the motion of dislocation at the surface, making their move under a stress gradient severe. The plasticity of the material is thus severely reduced, rendering the solid brittle.
According to researchers, this leads to the mechanism of the surfactants action in drilling. But this may not be the case in tumbling mill grinding for some reasons. In the first place, plastic flow is not an important criterion in tumbling mill. Also, in impact fracture, the rate of dislocation movement is a lot slower than in crack propagation.
Arguments abound to attest to the fact that grinding aids readily meet the needs of the valence forces formed during material fracture. Been polar substances, grinding aids are preferentially adsorbed on certain specific sites where the breaking of electrovalent or covalent bonds leading to residual electrical forces. This is what is partially responsible for the improved efficiency of wet grinding about dry grinding as water bipolar in nature.
In particular, cases, when the grinding aids are adsorbed by the particles, it results in the formation of similarly charged particles, which implies that repulsion experienced between the particles may be the reason for their dispersion.
It is also believed that grinding aids that could chemisorb on solid particles would significantly reduce the adhesive propensities between the particles thus resulting in improved grinding efficiency. And since these adhesive forces depend on the surface area, the grinding efficiency is higher, and the product size produced is finer.
In conclusion, the application of grinding aids requires them to be injected into the grinding mills, where adhesive forces are results in obstruction. So they could be used to an advantage, even if the grind is coarser.