Cut Your Machining Costs: 4 Ways to Save on Industrial Cutting Materials
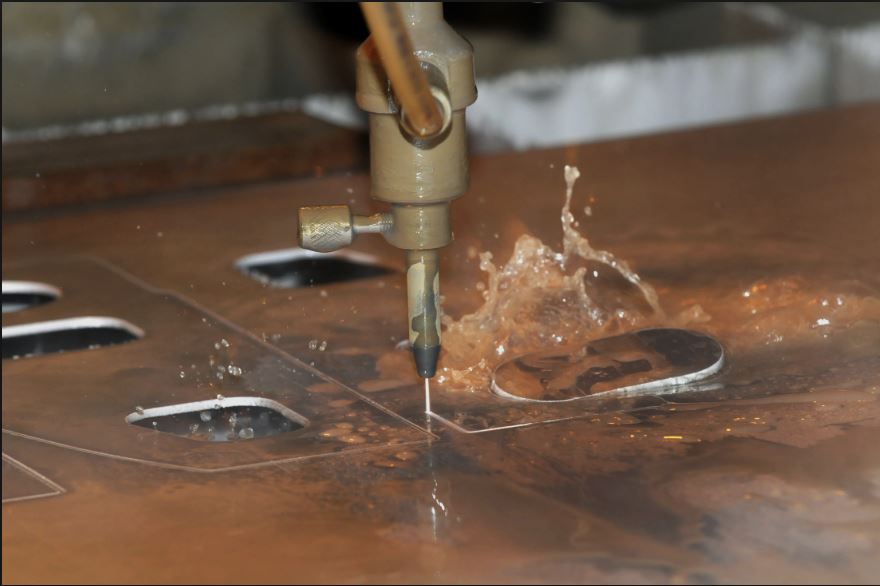
If you own or operate industrial metal cutting machinery, then you need to keep your operations running smoothly and get projects in under budget. However, this can often be harder than it seems, as unforeseen delays and costs can come in the form of machine failure, material replacement, and inefficient systems. Luckily, there are a number of tools and strategies you can use to make sure you are getting the most out of your machines in terms of time, money, and quality of production. Here is what you need to know to cut machining costs once and for all.
A barrier filter is simple in concept. It is the physical layer that prevents large chunks of debris from entering the cutting process or staying in the final mold. These contaminants can lead to deformities and other issues that slow your cutting line down, result in wasted material, and require an intensive machine cleaning and repair. Filters are a must, and each has their own lifespan that needs to be adhered to for quality results. Always replace your filters on schedule and have at least two spares available per machine at all times if you want to avoid unscheduled downtime.
Spinning metal and liquid at high speeds is yet another method your machines utilize to keep debris at bay. It separates them into other areas that funnel down into a tray, allowing for easy disposal of excess material. Keeping this system clean and maintained at all times, therefore, is a must. Spinning components are prone to wear and should be checked regularly to ensure that nothing is becoming loose on the axel, which would result in uneven spinning and less than desirable results. To prevent that wear, ensure that all of the components are properly lubricated, as well. This will both give your components a longer lifespan and allow your system to reach greater operation speeds with less energy required to get it there.
Skimmers are may seem like glorified metal-catching nets, but they are also important parts of the process. When something is too heavy for your screens, they need to be fished out, and if your skimmer heads are warped or there are tears in the netting, then it will significantly increase the time required to catch anything. It also increases the chance of dropping what has been caught, and the process starts over again. Dirty netting will create significant drag, as well, as the liquid won’t be able to pass through as easily. Your skimmers need to be regularly cleaned and repaired when damaged, or better yet, replaced. Losing time and money on this manual process is completely avoidable with the proper foresight and care.
If you don’t have a system to monitor the liquids that are used to lubricate the cutting process, then you are going to experience a number of issues down the line. When metal goes on metal, it is going to produce friction. This friction needs lubrication via the use of the right industrial cutting fluids, both for the same of the machinery and for the sake of your product. Getting the very highest quality industrial cutting fluid is important for keeping your machine running at peak efficiency. Still, having the best cutting oil is not enough by itself. Bacteria can build up over time and contaminate the quality of any oil. You could create a schedule for oil replacement based on old data, but doing so is inefficient and inaccurate if you really want to prevent contamination from spreading while also getting the greatest use of your oil. There are machines and systems designed specifically for the purpose of monitoring the oil for contamination and alerting you the moment there is any significant decrease in quality, allowing you to prevent the spread of the contamination without throwing way good oil.
The world of manufacturing and machining has never been more competitive. Long gone are the days where you were only competing with local suppliers. You now have to go head to head with the best and most organized machine shops around the world, competing to provide the best products at the best prices. Keeping your systems well maintained for efficiency and longevity is essential to keeping your overall costs low. Don’t cut costs in the cutting room, and you may not need to cut costs at all.