Warehouse Safety Tips
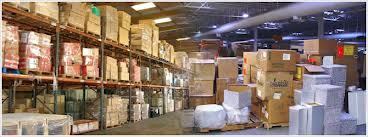
Whether you realize it or not, there are many potential safety hazards inside every warehouse in the country. Your job as a business owner or company manager is to reduce these risks by providing a safe environment for all of your workers. The first place to start when determining what safety measures to implement in the workplace is OSHA (Occupational Safety and Health Administration). OSHA is operated by the federal government and sets specific rules and regulations that must be followed in the workplace. You must first understand all of these rules to create a safe working environment for your company.
Warehouse Hazards
To properly set warehouse safety standards in place, you must first recognize what the potential hazards are in the warehouse environment. According to OSHA, the risk of having a fatal injury happen in a warehouse environment is higher than the national average for other types of employment. This means that you must take special care to insure you warehouse setting meets all the necessary safety rules. OSHA also lists some of the main warehouse hazards as forklifts, storage, problems with electrical wiring, potential fall risks, and failure of employees to use protective equipment
Safety Tips
Now that specific warehouse hazards have been recognized, you can look at some of the warehouse safety tips that will make the workplace safer and reduce the risk of injury.
These vital warehouse safety tips will improve the safety conditions in your workplace and reduce the overall risk of injury. This, in turn, can lead to increased productivity and reduce costs. Proper training on all the company’s safety regulations is key to successful implementation. Training your current workers and new hires should become a priority for you company.
Written by the team at Premier Warehousing Services.