Industrial Warehousing: 7 Things You Need To Be Successful
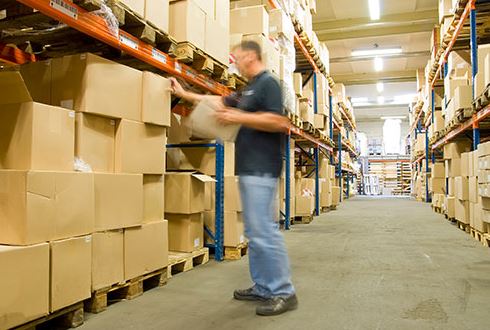
Running a warehouse involves much more than just providing space for someone, including you, to store stuff. You have to be able to store things safely, access them quickly, and keep track of everything efficiently. There are many things that are crucial to this process, but the following seven are the most pertinent.
Instead of having your employees walking around with clipboards and pens, give them electronic means. The easiest option here is using bar-code scanners. You can program the scanners to track incoming material as soon as it arrives and also when it’s moved around inside the warehouse. Another option is radio frequency tracking. With this method, each item is assigned a specific radio frequency. Both methods are far more efficient than writing things by hand.
Basically, this strategy means: Always call a widget a widget. When you select a SKU for a part, it’s best to use that particular SKU all the time, particularly if you have more than one warehouse. That way, two employees separated by hundreds of miles can each use a bar-code scanner to track two pallets of the same item in two different locations in real time instead of spending time on the phone figuring out what’s where.
Categorize every item that comes into the warehouse. Group those items into separate areas by category. The goal of such categorization is to make it easy for a new hire to grab a scanner, walk onto the floor of a gigantic warehouse, and find the part or parts he or she seeks as quickly as possible. Also, in much the same way as you use standard SKUs between locations, your bin location strategy should be identical at each of your locations. Such uniformity breeds efficiency, which, in turn, breeds profitability.
You won’t need every product all the time. It doesn’t pay just to “keep that one pallet in case we need it.” Every product on the floor should be needed to fill orders. By keeping accurate track of all SKUs, you’ll know what’s needed and what’s not.
You’re going to need forklifts, overhead cranes, high-quality shelving, and other material handling machines and storage solutions. Don’t skimp. The best equipment, such as that provided by American Equipment Inc., is almost always the safest equipment, too, so you accomplish two goals with one choice regarding equipment: safety and efficiency.
People who work in safe environments trust both each other and management much more than they do in unsafe environments. By reinforcing the safety of every employee, you make the employees feel valued. At a purely monetary level, a safe environment reduces loss because items of any kind don’t get broken.
The world of 21st-century business, particularly the material handling business, is ever-changing. What’s hot today might not be hot tomorrow, and vice versa. Processes considered safe last year may be subject to new regulations this year. Take these changes in stride and treat them as opportunities for growth. Not only will you save yourself gray hair, but you’ll also increase profitability.
These strategies are not difficult to implement, and the returns they generate will more than offset the costs of their implementation. Most of them are common sense too.