How Quality Is Related To Failure: Latest Industry Developments
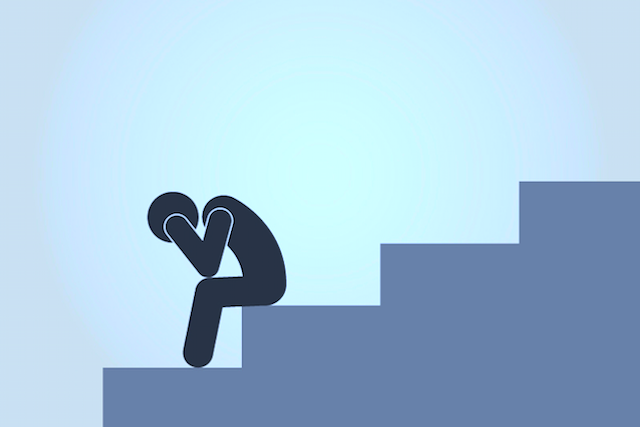
Failure can be the best teacher. In a supply-chain setup, failures can help turn operations a new leaf by adding and refining the metrics. They can expose deficiencies in existing metrics and improve processes. But not addressing failure makes it necessary to have expensive training-on-hazard models, while the risk remains.
Although positive points about failure can be described in detail, what’s more important is that for benefits to really show up, one must achieve accurate insights from reliable data. If one can interpret failure better, the insights can always be used to fine-tune existing benchmarks and create more realistic ones for supply-chain participants.
While failure data is definitely one part of the puzzle, more and more sophisticated data-management systems implies a massive increase in the number of organizations looking to leverage the power of data feeds. People are finding low-latency data to be highly valuable in fine-tuning benchmarks in supply-chain logistics.
The power of low-latency, real-time can be easily seen with user experience, which certain hyper-local logistics companies are delivering to end users. They can easily track the location of their items, which increases customer trust and repeat rates. The same data can actually be used to fine-tune benchmarks also.
Let’s take an example
Suppose a food-delivery network wants to set a benchmark for the average time deliveries take. The best way may be to dynamically decide a benchmark based on crunching the rates of deliveries happening on the city network in real time.
The experiment can be repeated multiple times to find the expected error margin, and narrow down more on the accurate mean. Thus, by using real-time data, the food delivery network should be able to set for itself, a realistic benchmark, which is data backed and rigorously standardized. The company can then keep running the experiment and detect anomalies easily.
How can failure data be used to create new benchmarks? Failure can be used in two ways to create new benchmarks:
Let’s talk about the first case. Failure data can be used to make the already existent benchmark, to be more heavy-tailed and hence, more robust to outliers. Usually, systems can take a count of the failures happening which can then be appropriately weighted as per the deviation from the current standard. These weighted failures can then be used as “skewers”, which are responsible for either pushing the benchmark to the left or to the right.
More the failure data, more accurate the benchmark becomes!
If we are getting failure data in real time, the skewing process can actually run continuously in real time too, making the benchmark much more realistic every day.
In the second case, real-time data can be used to calculate means and the error margins while it can be mixed with failure data, which can act as a skew for the incoming stream. Thus in this case, we can create new benchmarks, even when we do not have existing ones.
Small glitches lead to big losses in supply chains, as they rely on mutual trust between partners. So it is useful to have “mutual cooperation” understood delicately. Intent to innovate for a better understanding in the management department follows that failure-data processes are becoming simpler and easier to use and understand. IT platforms in manufacturing units are changing the way people perceived industries to operate and leverage.