A Step By Step Guide To Running Your Own Warehouse
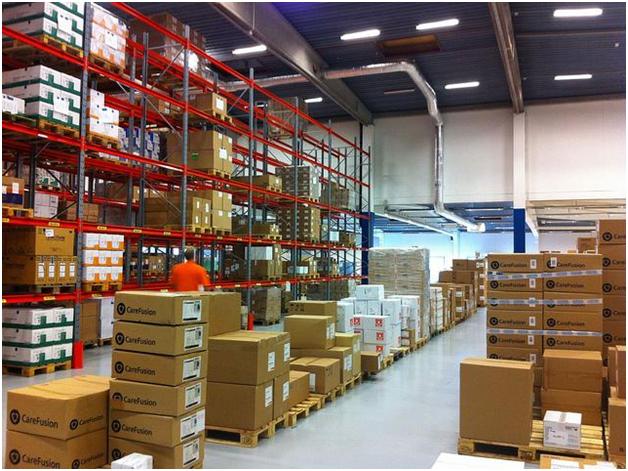
Regardless of what your company specialises in, if you hold lots of stock you’ll have to purchase or rent a warehouse at some point in the future. This may sound like a simple move, but it’s likely to open your business to a whole load of new issues you’d never even considered before. The warehouse environment is completely different to that of a traditional office, and so your approach should be tailored accordingly. With that in mind, I’ve decided to release this post today in the hope of helping you to navigate the expansion without encountering too many problems.
You see; I spent well over ten years working in warehouses around the UK, and during that time I managed to rise from being a simple order picker to manager on more than one occasion. This is something you should aim to replicate with your own staff members because people who’ve spent time working on the shop floor are the ones most likely to introduce effective policies and procedures that will create optimum profit. So, if you want to learn a bit more about running your own warehouse, here’s a step by step guide to get you started…
Depending on how profitable your business is and how widely you’re expanding, the decision on whether you buy or rent should be a simple one. However, locating the perfect premises may not be. Thankfully, there are many websites online nowadays that list commercial buildings for sale and rent, and most of which are reasonably reliable. I’d advise you spend some time looking through all the options available before settling on your final choice.
It’s always wise to employ only the most experienced individuals to begin with, as they’re the ones most likely to identify any issues with your plans and make you aware of them. Also, advertising warehouse jobs on government-run job boards will usually result in your receiving thousands of applications from unsuitable candidates – something you obviously want to avoid at all costs. If at all possible, try headhunting staff from other local firms, or look for companies that have recently made redundancies and see if you can find out what happened to their team.
Once you start receiving stock into your warehouse, you’re going to need to purchase some adequate racking and other storage devices. Likewise, you’ll need to get in touch with SHS Handling or another reputable company to source pallet trucks, trolleys, forklift attachments and whatever else you’re going to need. Presuming you do this without too much hassle, you’re almost ready to start using the warehouse as part of your operations.
Lastly, you need to spend some time with a professional walking around your warehouse and identifying any potential safety risks. Then it’s time to start drawing up policies and procedures that will ensure these risks are minimised. This is all pretty self explanatory, but if you have trouble performing this task, simply call in the experts. There are plenty of firms out there who specialise in risk assessment, and they’re be more than happy to help.
So, there you have it my friends. Now you’re ready to open your warehouse and start making even higher profits than you were previously. Just make sure you don’t rush things, and you should find all your day to day operations run smoothly.
Good luck with the expansion, I hope it goes well for you.