More Optimized Supply Chain Means More Cost Cuts and More Profit For The Company
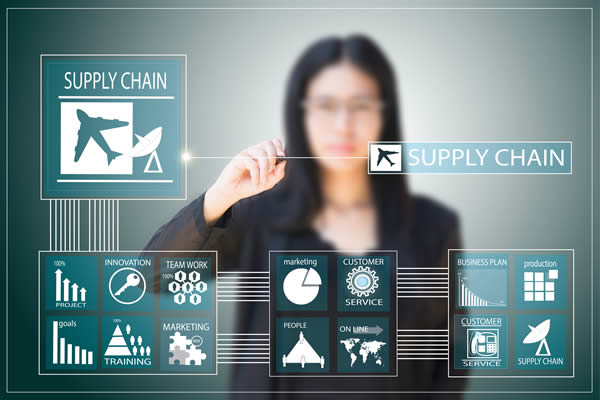
Supply chain optimization refers to the overall processes aiming at obtaining significant and quantifiable benefits in terms of reduced inventory and lower logistics cost while typically maintaining or improving customer service through better forecasting and improved availability. Supply chain optimization involves steps for better and optimum utilization of items for better results. This includes measures like maximizing gross margin return on inventory, balancing the cost of inventory at all the stages in the supply chain with availability to customers, and minimizing total operating expenses, i.e., of transportation, inventory, and manufacturing. It should also factor in unforeseen events, such as fire or an earthquake affecting the manufacturing processes and jeopardizing the supply chain planning. Supply chain optimization gains prominence due to volatility in the economic scenario across the globe.
Below are some steps and benefits associated with Supply Chain Optimization.
The paper-based purchase order and approval system consumes a lot of buyers’ time and at times creates a sense of frustration among valued customers. Therefore, opt for paperless procurement via the introduction of Web-Based Central Purchasing System. This will help a business to expedite the approval process, centralize the international procurement, and quicken up the organization’s supply chain optimization process as compared to maintaining those paper-based POs and approval records. Moreover, with the data generated, vendors can be rationalized/categorized, and contracts can be negotiated much better, as the complete update in real-time and a complete financial picture are available with easy access.
A sales team should be involved in demand forecasting and inventory planning on a regular basis. Accurate sales forecast would enable a business to implement the Collaborative Planning, Forecasting, and Replenishment (CPFR) process with key suppliers to reduce inventory storage requirements to a minimum level.
This would help in tracking and updating global inventories and maintaining a database of suppliers, which could be used to categorize suppliers in terms of fulfillment time and price.
Direct Plant Shipment (DPS) or direct shipment is a method of delivering goods to customers directly from the plant. In this process, strategically located regional centers provide overnight shipments to the maximum number of customers. This delivery scheme reduces transportation and storage costs.
Pursuance of the above-mentioned steps will result in reduced number of supply chain employees, proper tracking, and management of all supply chain links from a single office. The basic idea is a more optimized supply chain will result in more cost cuts and more profit to the company.